3维打印降低了75%的砂型铸造成本
借助3维打印可将模具和核心的生产流程大幅度缩短。相比之下,如果传统工艺法的成本在3600欧元,那么使用3维打印法生产同样部件的成本可降低至900欧元。借助3维打印可将模具和核心的生产流程大幅度缩短。某些步骤可被节省,如昂贵的工具成本,因为生产砂型模具和核心只需CAD数据的记录。
砂型模具、核心部件和小系列产品可不需使用任何工具并经济化的被生产。和传统工艺相比,3维打印针对模具和核心的复杂程度基本没有界限可言,因为3维打印的步骤和部件的复杂程度无关。
在制造涡轮砂型核心时,此因素非常重要。传统工艺必须将涡轮叶片的单一核心部分非常麻烦的组合成一个核心,而3维打印方法可以将涡轮核心作为一个整体打造,所以整个生产流程明显缩短。因此即节省75%的成本,也保障了高质量并精确的成品。
经济化的生产模型和小系列产品
极短的交货时间和满足各种需求的灵活性是非常重要的。但是,这两个因素可以有意义并经济化的互相结合吗?
砂型模具和核心可在短短几天内完成。和传统工艺相比,这可节省很多个星期。此外,提高了多方面的灵活性。其一,不需要注意底切或脱模斜。其次,必要的铸造设备可以直接被设计并打印入成型框内,如浇道系统。组件的变化也可快速并简单的实施。我们的目的是节省模型和核心制造的时间和成本,并简单的实现复杂的几何。在此,混合结构可根据3维打印和传统工艺的结合随意地被利用。
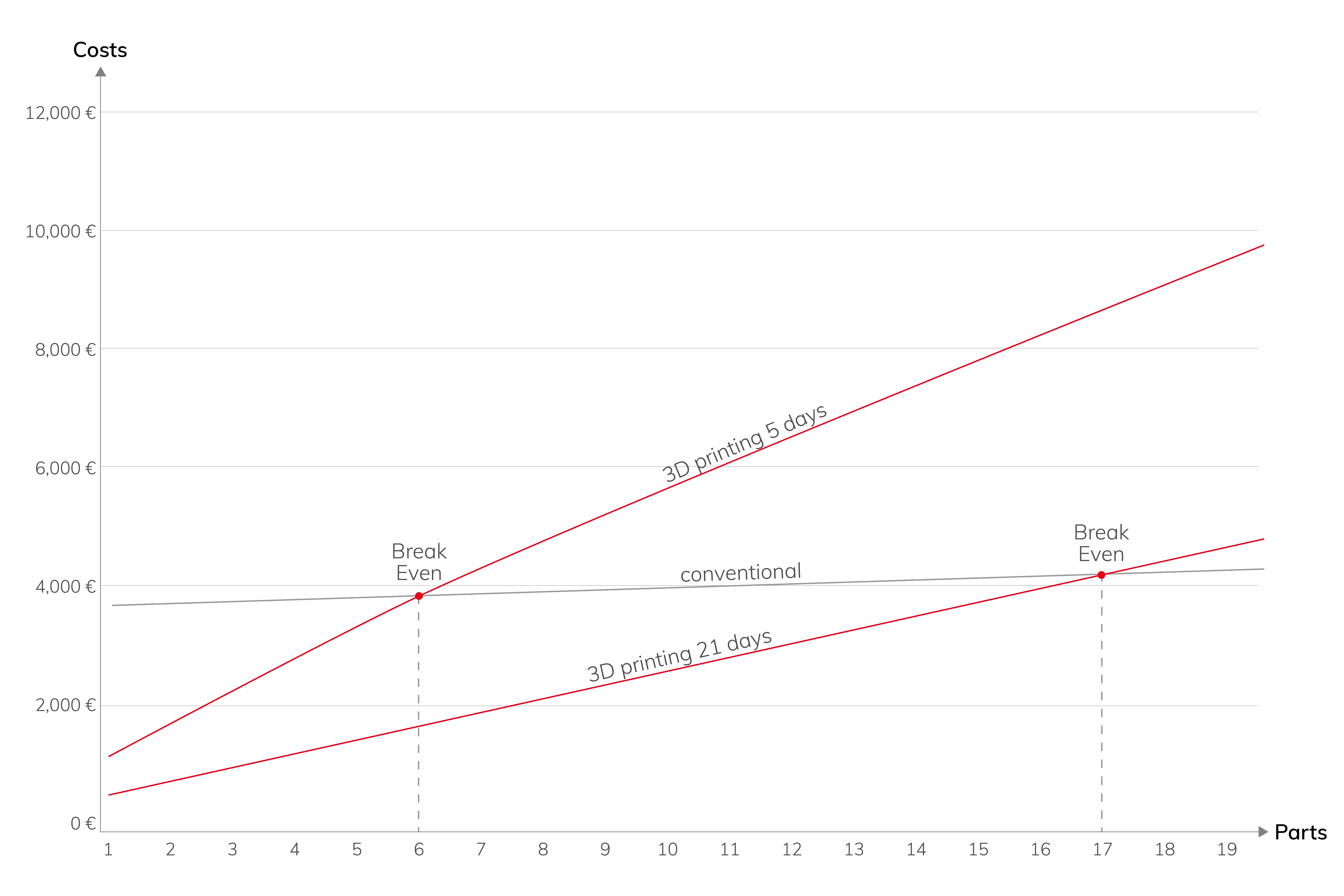
从被打印的核心到最后的成品铸件
3维打印:
各种复杂的砂型模型和核心由一个层次打造流程完成。在此,一个转发器将颗粒材料细层的分布于整个施工面。一个按钮将粘合剂选择性的分布于部件将组成的方位。这两个步骤反复执行,直至完成部件。之后,松散的颗粒材料被清除,并作后加工。
修整:
如同传统的砂型铸造一样,为了承受高温,被打印的核心要被修整。
核心安装:
之后,3维打印的砂型核心被置入一个传统的模具内。混合制造法可将打印的和传统的模具随意的结合。
铸造:
此时,涡轮被铸造。通过3维打印的模具和/或核心可以由各种常见合金铸造。各种不同的沙粒可影响不同的表面光洁度。
核心脱模:
如同传统的制造法一样,3维打印的砂型模具和核心在铸造后也需脱模。
后加工:
脱模后部件需被加工,但是使用3维打印工艺的后加工要简单很多,因为铸件更精确,这是由于复杂的几何是整个带底切被打印的。
3维打印的优势
- 通过短的生产时间和免工具生产,节省了时间和成本。
- 在件数和模具设计方面具有高度灵活性。
- 通过与传统工艺相结合的方式进行混合设计。
- 传统砂模和砂芯没有储存和维护成本。
进一步的案例研究
PMMA 三维打印技术征服北美
Express Prototyping 是北美投资铸造模型三维打印领域的领先专家之一。了解总经理 Thomas Müller 如何创建公司以及他对未来的展望。
博罗铸造厂 – 过热器集束器
英国铸造厂Boro Foundry利用砂型和3D打印的结合,为蒸汽机车生产了一个无缺陷的备件。
底盘摆臂的优化
农业机械制造商Amazone使用Altair的模拟软件和voxeljet的3D打印技术来优化一个转向架底盘。